e3 Harold Kerzner 項目管理 v12
20.5 7個質量控制工具
最近幾年來,統計方法在商業、工業和科學等領域都比較流行。在可以進行聚類、製表和分析數據的高級自動系統的幫助下,這些定量方法的實際應用也在不斷髮展。
比定量方法本身更重要的是它們對商業基本思想的影響。它們提供了在定量事實基礎上進行客觀決策的基礎,使得決策排除了主觀獨裁決策的做法。這些變化會帶來特有的好處:
• 改進處理信息。
• 改善溝通。
• 在事實基礎上進行討論。
• 在採取行動前要達成一致意見。
• 過程變化的信息。
統計過程控制(Statistical Process Control,SPC)利用了過程的自然特徵。所有的商業活動都可以用已知公差和可測變差的特殊過程來描述。這些變差的測度和信息結果可以為連續的過程改進提供基礎。這裡所說的工具提供了過程數據的圖形表示和測度。系統地使用這些工具有助於企業控制生產過程和產品,使其具有世界競爭力。
統計學的程序控制基本工具是數據表、帕累託分析、因果分析、趨勢分析、柱狀圖、散點圖及控制圖。這些基本的工具為有效的資料收集提供了服務,可以對資料中的模式進行辨析,並對可變性做出測量。圖20-6展示了這7個工具之間的關係,以及它們對改進機會的辨析和分析功用。下面我們將評論這些工具,並討論它們的操作和應用情況。
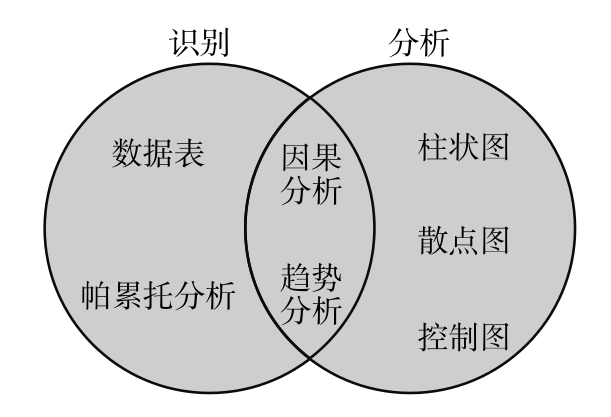
圖20-6 7個質量控制工具
20.5.1 數據表
數據表和數據隊列為數據的分類和展示提供了系統的方法。大多數情況下,數據表是為進行數據分類而編制的表格。當數據來源於自動媒體時經常用到這些表。它們提供了收集數據的一致、有效和經濟的方法,將這些數據組織在一起進行分析,以及為了簡單地討論而進行展示。當沒有自動數據時,數據表經常以手工表格的形式出現。數據表或檢查表應該設計成需要最小輸入信息的樣式。簡單易懂、直觀的表格是成功數據聚類的關鍵。
圖20-7是一個確認發貨單屬性(有效/無效)的例子。從這個簡單的檢查單中可以很明顯地看到幾個數據點:總錯誤次數是34、錯誤最多來自供應商A、最常出現錯誤的是試驗記錄。利用帕累託分析、控制圖和其他統計工具,我們可以對這些數據進行進一步分析。
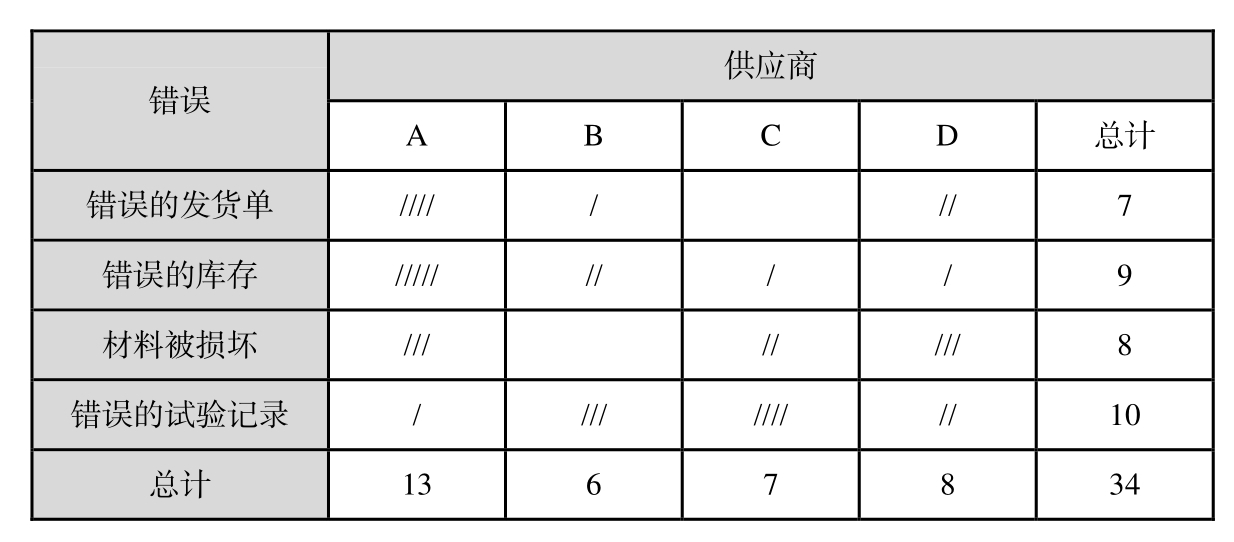
圖20-7 材料接收和檢查的核對表
20.5.2 因果分析
確定問題後,我們有必要分析其原因。因果關係有時是模糊的,為了確定問題的一個或幾個具體原因,經常需要大量的分析。
因果分析用圖形技術來確定原因和結果之間的關係。因果圖也被稱作魚骨圖。圖20-8為基本的魚骨圖。進行因果分析需要6個步驟。
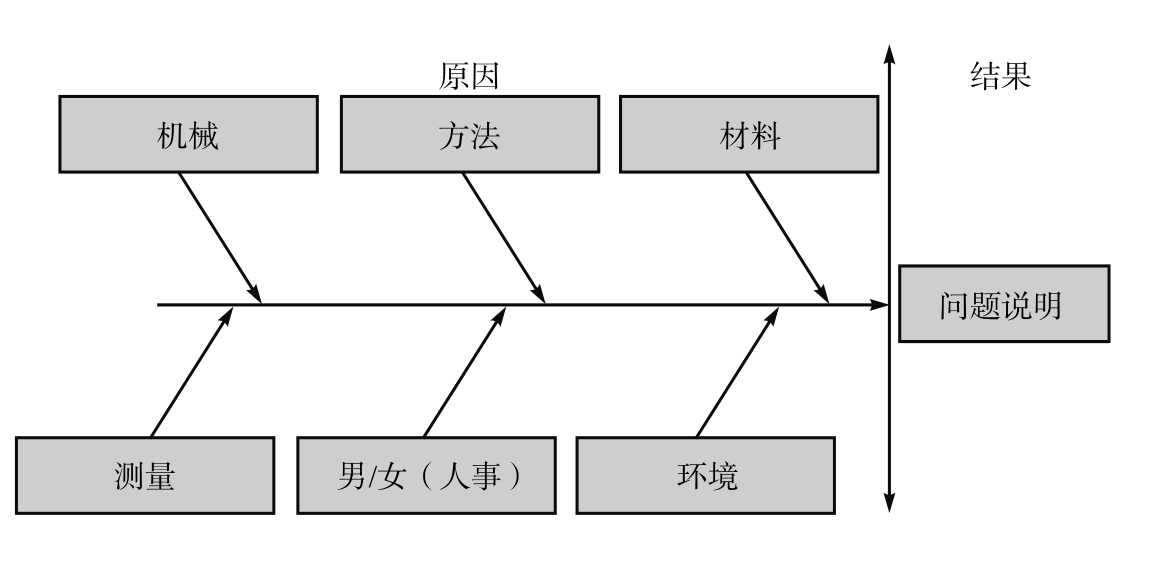
圖20-8 魚骨圖
步驟1 確定問題。 這個步驟經常包括其他統計過程的控制工具,如帕累託分析、柱狀圖和控制圖,以及頭腦風暴法。其結果可以對問題進行簡潔、清晰的描述。
步驟2 選擇各學科間的頭腦風暴團隊。 按照確定問題的原因所需要的技術、分析和管理知識來選擇不同學科的專家組成頭腦風暴團隊。
步驟3 畫問題箱和主箭頭。 這一步包括用於因果評價的問題說明。主箭頭作為主要類別的分類基礎。
步驟4 具體化主要分類。 確定問題箱中所說問題的主要類別。問題所產生的主要原因的6個基本類別是人事、方法、材料、機械、測量和環境,如圖20-8所示。其他類別可以具體化,視分析需要而定。
步驟5 識別問題原因。 識別出問題的主要原因後,可以分別就每一主要分類的相關原因進行分析確定。這一步驟的分析有3種方法:隨機方法、系統方法及過程分析方法。
1)隨機方法。列舉同時導致問題的6個主要原因,確定同每個類別相關的可能原因,如圖20-9所示。
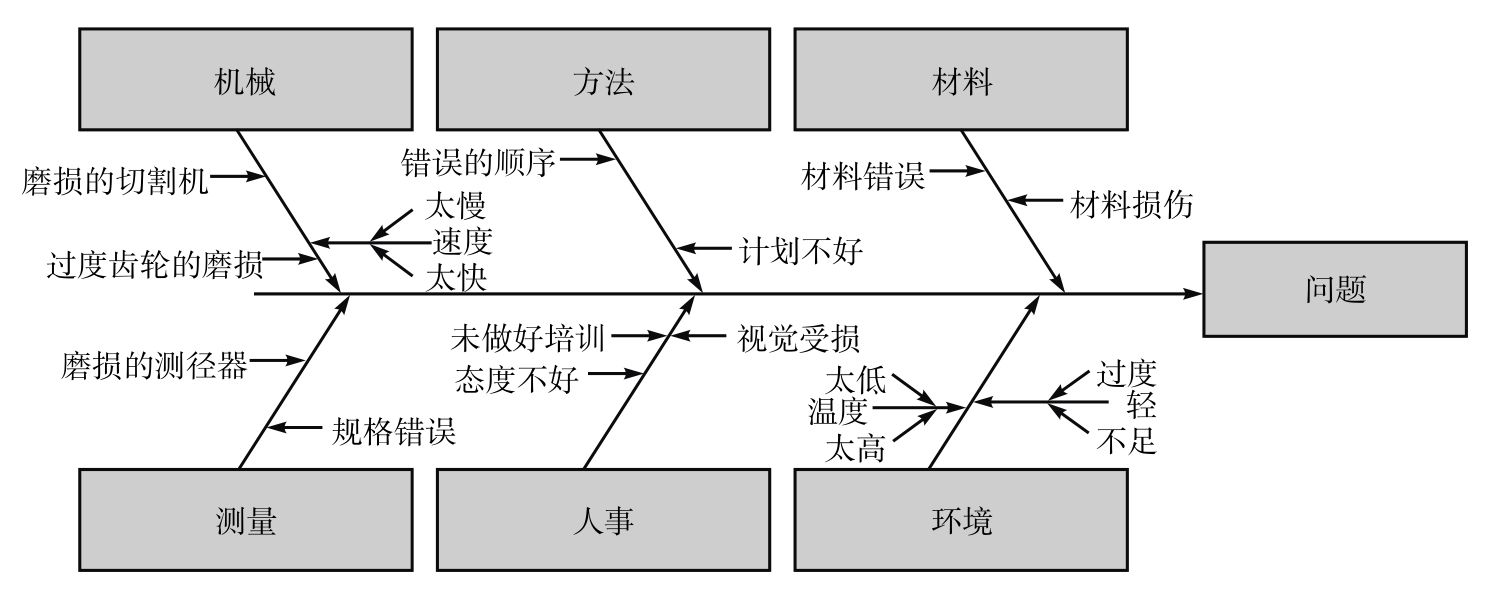
圖20-9 隨機方法
2)系統方法。按照重要性的降序排列,一次著重分析一個主要類別。只有當完成了最重要的一個類別之後,才能轉向下一個次重要的類別。這個過程如圖20-10所示。
3)過程分析方法。確認過程中的每個序列步驟,在每一步進行因果分析,一次一個步驟。圖20-11說明了這個方法。
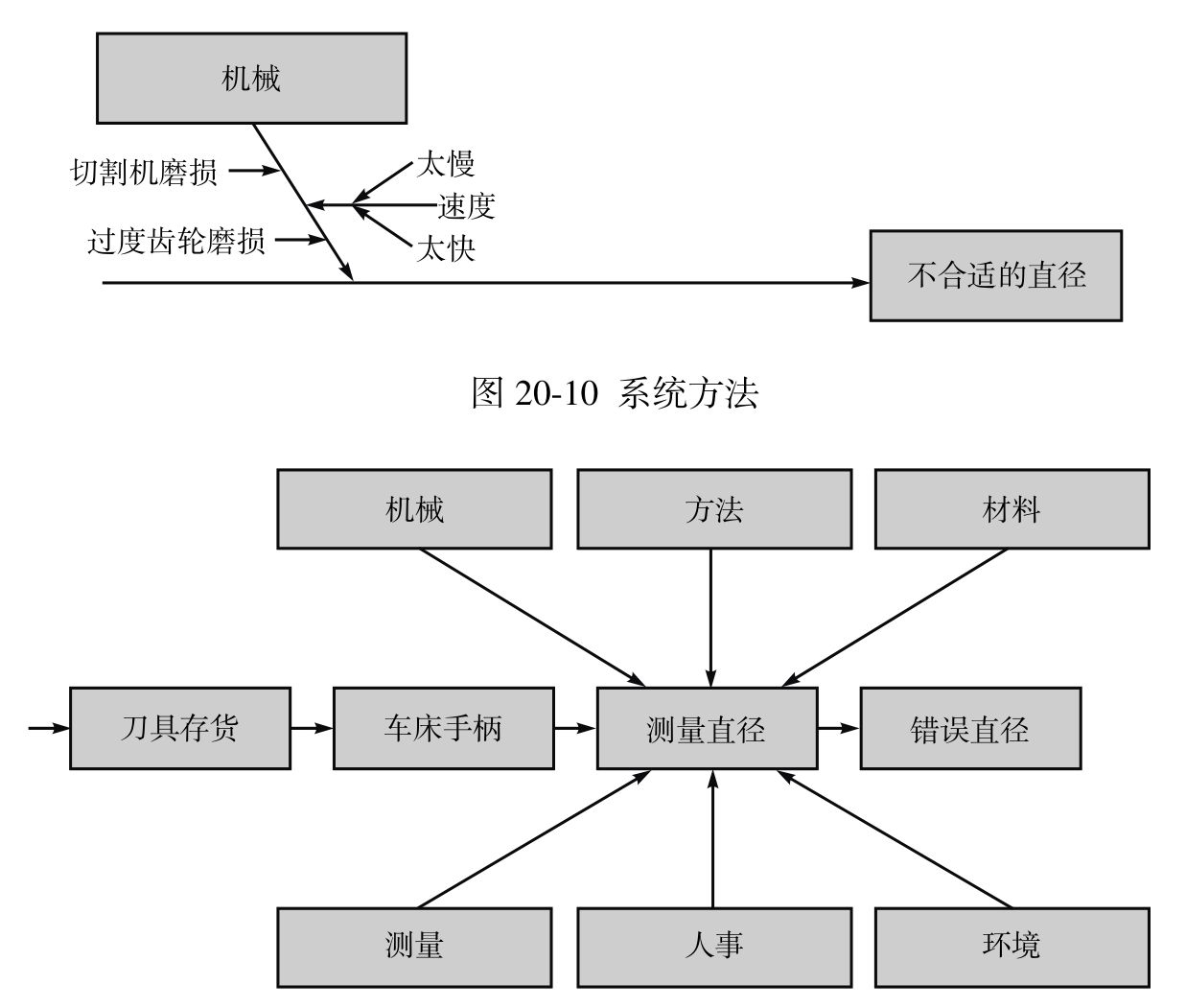
圖20-11 過程分析方法
步驟 6 確認矯正行動。 這包括兩步:① 問題的因果分析;② 確定導致每個主要類別的原因。在這兩個步驟的基礎上確認矯正的行動。矯正行動分析同因果分析的方式一樣。將因果圖反向,問題箱就成了矯正行動箱。圖20-12表示了確認矯正行動的方法。
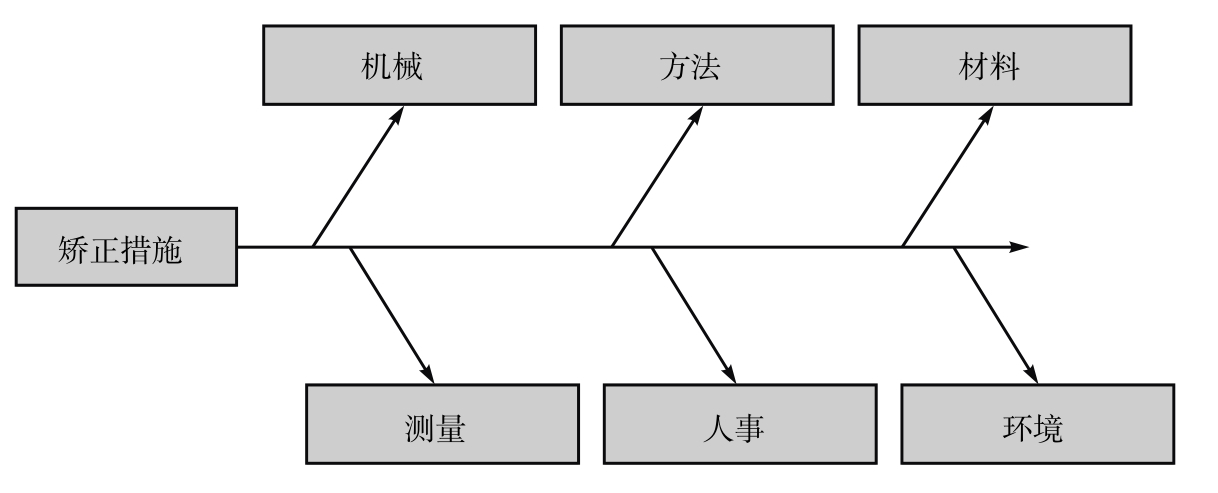
圖20-12 確認矯正行動
20.5.3 柱狀圖
柱狀圖是用於描述數據頻度分佈的。這個工具對於評價數據屬性(對/錯)和變量(測度)是很有價值的。柱狀圖對在某一時間點的數據提供了簡潔的展示,它沒有給出方差或隨時間變化的趨勢,只展示了累積數據今天的狀況,理解數據的相對頻率(百分比)或頻度(數字),以及數據如何分佈時是非常有用的。圖20-13表示了生產過程中錯誤頻度的柱狀圖分佈。
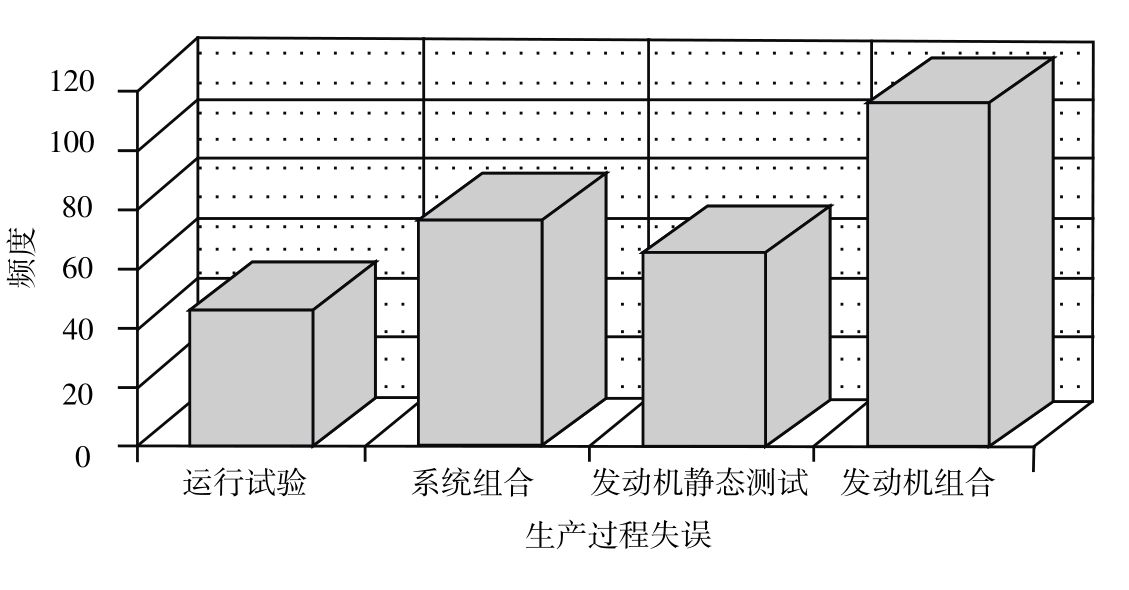
圖20-13 變量柱狀圖
20.5.4 帕累託分析
PMBOK ® 指南,第6版
8.3.2 控制質量:工具與技術
帕累託圖是特殊的柱狀圖,用於確定問題領域並對其進行優先次序的劃分。帕累託圖的建立可能包括圖形數據、維護數據、修復數據、部件廢品比率(parts scrap rates)或其他來源。通過確認來自這些來源的數據的任何不一致類型,帕累託圖能將注意力轉向發生頻率最高的元素。
帕累託分析有3種用途和類型。基本帕累託分析能夠確認導致任何系統大多數質量問題的幾個主要原因。比較帕累託分析集中於任意數量的項目選擇或行動。加權帕累託分析給出了因素相對重要性的測度,有些因素可能最初看起來並不重要,如成本、時間和危險程度等。
基本帕累託分析提供了給定數據集合中發生頻度最高的事件的評價方法。將帕累託分析步驟用於圖20-14所示的材料接收和核對過程,我們可以得出如圖20-15所示的基本帕累託分析。這種方法量化和圖形化了材料接收和核對事件發生頻度,並在頻度基礎上進一步確定了最重要的因素。
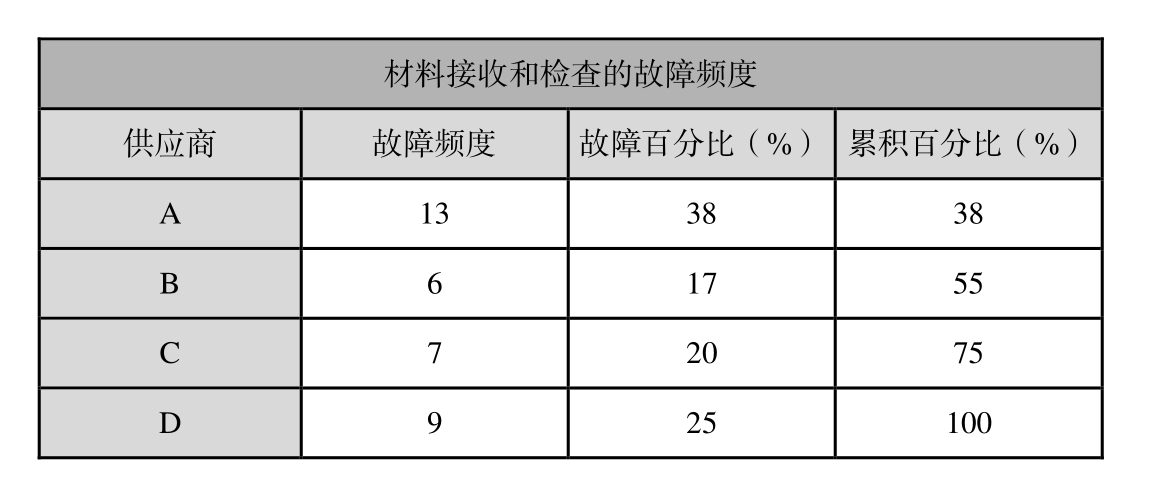
圖20-14 基本帕累託分析步驟
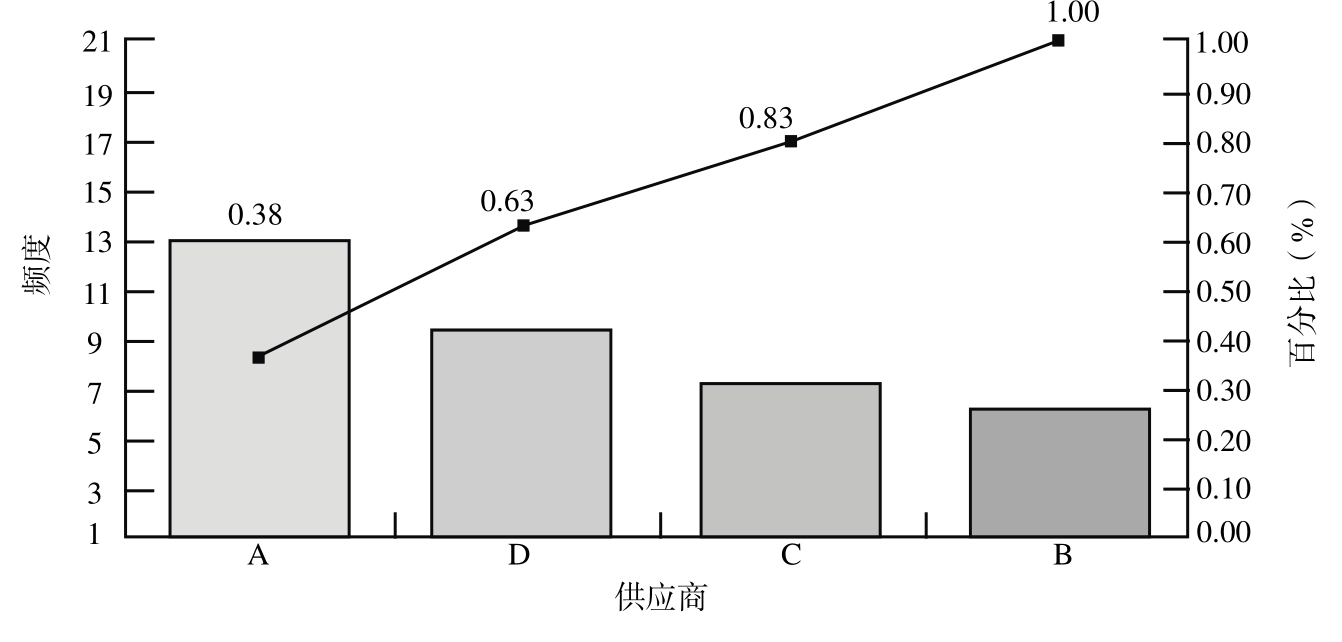
圖20-15 基本帕累託分析
對事件頻度應用基本帕累託分析方法討論,表明供應商A在所有的故障中所佔的比例最大,為38%。帕累託分析圖也用於確定矯正行動的影響,或者分析兩個或多個過程和方法之間的差別。圖20-16表示了用帕累託方法評估矯正行動前後的錯誤差別的過程。
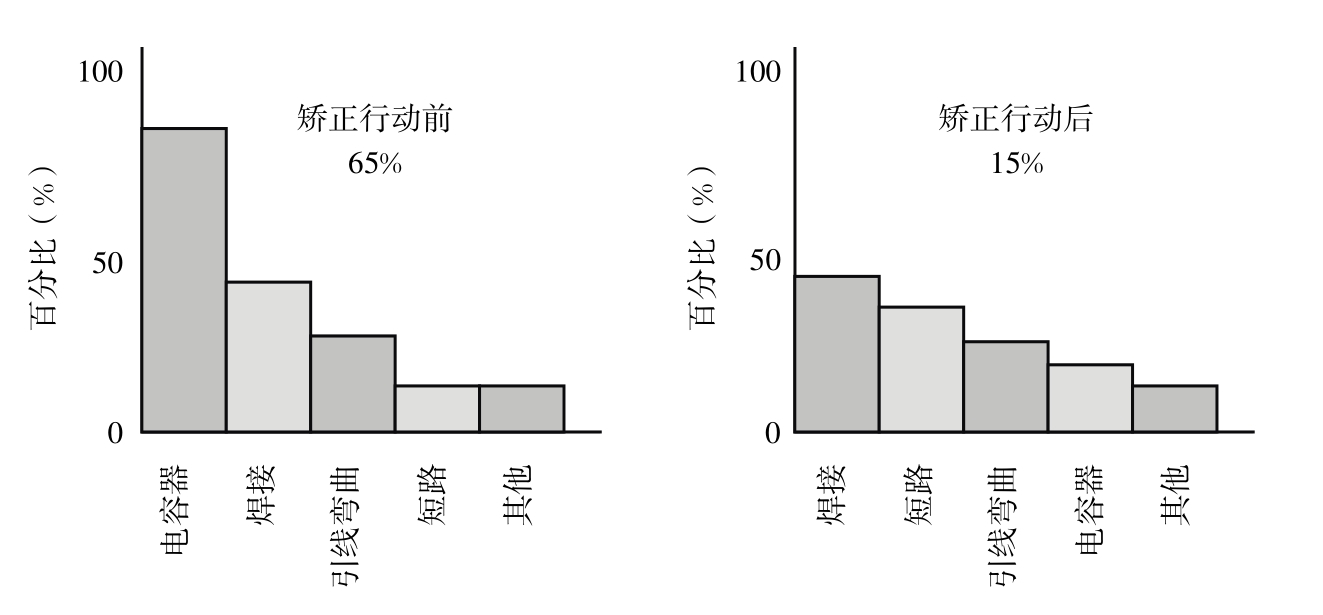
圖20-16 比較帕累託分析
20.5.5 散點圖
PMBOK ® 指南,第6版
8.3.2. 控制質量:工具與技術
另一種過程控制數據的圖形表示是散點圖或圖表。散點圖用兩個變量組織數據:因變量和自變量。這些數據在X 和Y 座標中表示變量之間的關係。圖 20-17表示了來自焊接質量試驗得分的兩個數據元素的相互關係,自變量月份用X 軸表示,因變量得分用Y 軸表示。
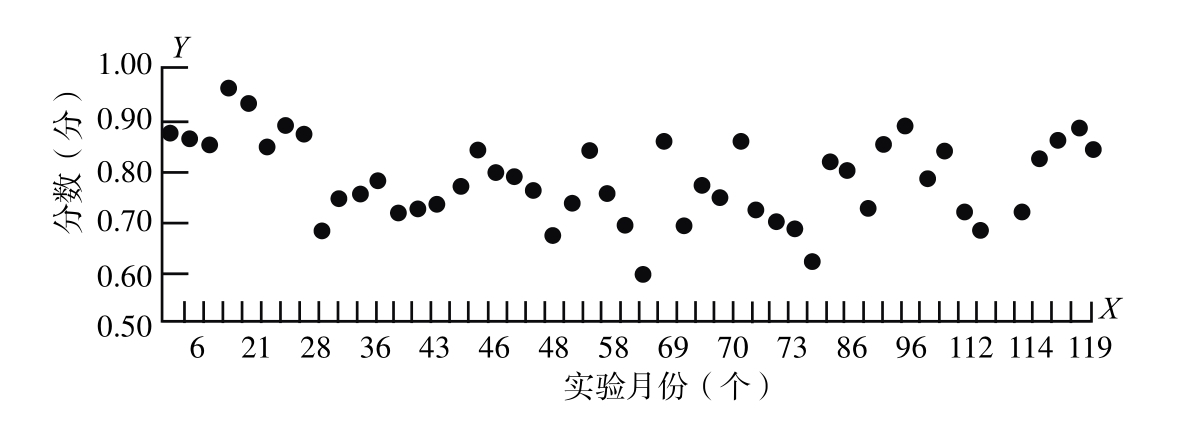
圖20-17 焊接質量試驗得分
這些關係可分成幾個類別,如圖20-18所示。在第一個散點圖中,數據無相關關係——數據點分佈分散,沒有明顯的關係形式;第二個散點圖是用U形圖表示的曲線關係;第三個散點圖有負的相關性,以一個向下傾斜的線表示;最後一個散點圖有正相關性,並且有上升的趨勢。
從圖20-17中我們可以看到,焊接試驗的圖有曲線的樣式,經驗最多和經驗最少的工人的得分最高,而那些中等水平工人的得分相對差些。下一個工具——趨勢分析將幫我們進一步清晰化和量化這些關係。
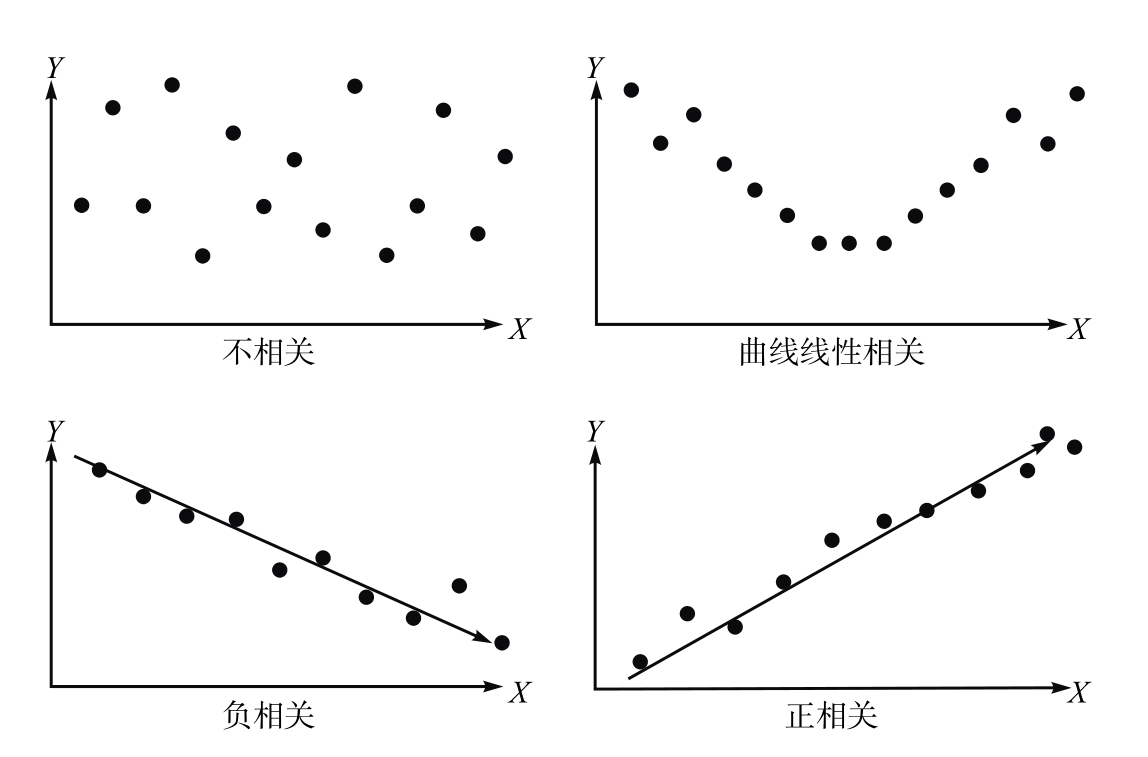
圖20-18 散點圖相關關係
20.5.6 趨勢分析
PMBOK ® 指南,第6版
8.3.2 控制質量:工具與技術
趨勢分析是在散點圖中確定最有擬合方程的統計方法。它量化數據之間的關係、確定方程,以及測度數據和方程之間的擬合度。這種方法也稱作曲線擬合或最小二乘。
通過提供因變量(輸出)和自變量(輸入)之間關係的方程,趨勢分析可以確定最佳的操作條件。焊接中經驗和得分之間的關係數據就是一個例子(見圖20-19)。
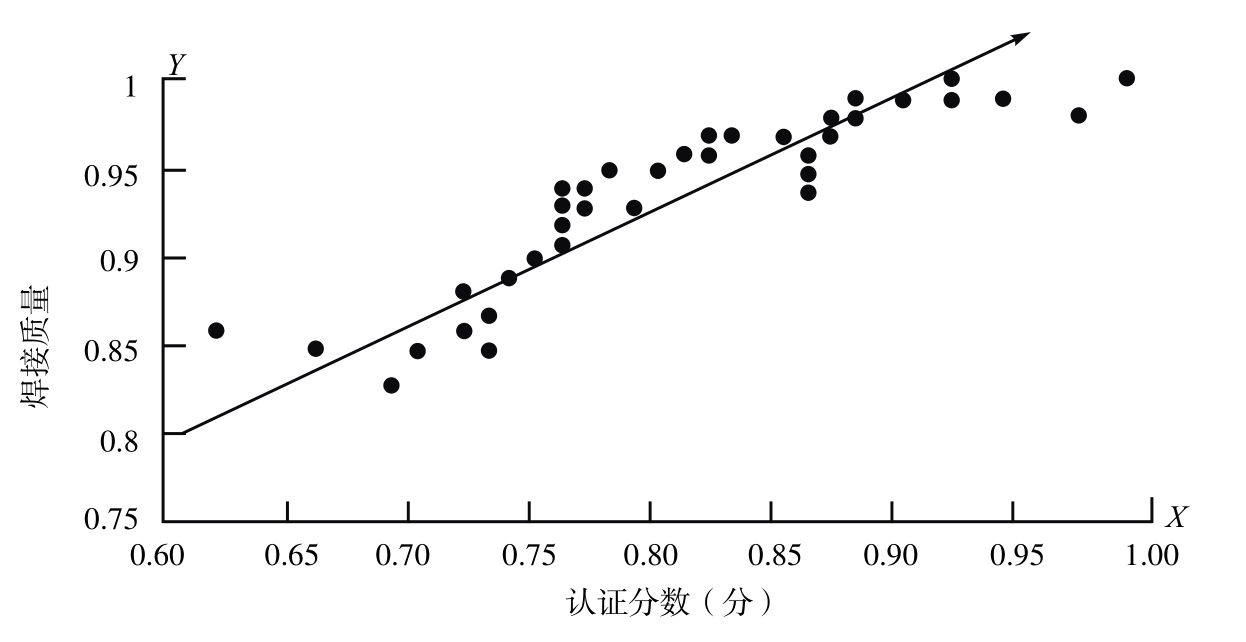
圖20-19 焊接質量散點圖和認證分數
迴歸線方程或趨勢線方程對自變量或輸入變量的每個增量變化所引起的因變量的變化提供了清晰易懂的測度。運用這一原則,我們可以預測過程發生變化後的影響。
趨勢分析最重要的貢獻之一是預測。預測可以使我們預知未來將發生什麼。根據迴歸線,當自變量的取值超出了現有的數據範圍時,我們可以預測將發生什麼。
20.5.7 控制圖
PMBOK ® 指南,第6版
8.3.2 控制質量:工具與技術
控制圖的用途主要是防止錯誤,而不是探測和拒絕錯誤。在商業、政府和工業中,經濟和效率一直是通過採取預防措施得到的。生產一個令人不滿意的產品或服務的花費要遠遠多於生產一個令人滿意的產品。提供客戶不滿意的產品或服務會花費大量成本,包括勞動、材料、設備和客戶量的損失。
應用統計過程控制圖可以大大降低生產合適產品的成本。
1.控制圖和正態分佈
控制圖的建立、應用和解釋是建立在正態分佈基礎上的,如圖20-20所示。控制圖的中心線代表數據的平均值( );控制圖的上下控制限(UCL和 LCL),分別代表均值加減3倍的方差
小寫字母s 或希臘字母σ 代表控制圖的標準差。
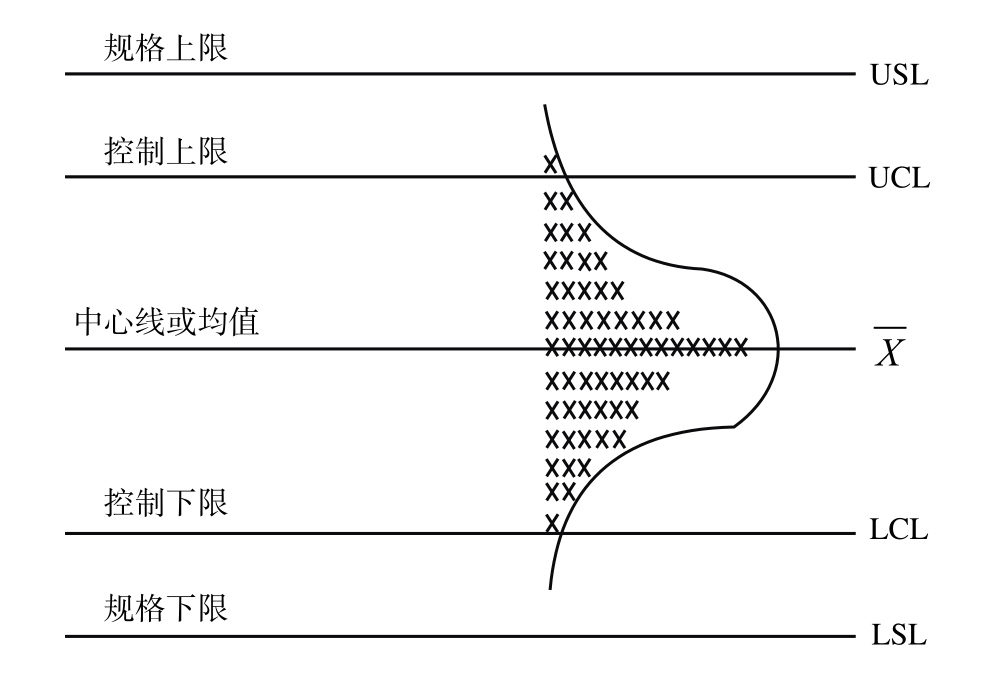
圖20-20 控制圖和正態曲線
正態分佈和它對控制圖的關係用圖的右半部分表示。正態分佈可以完全用均值和方差來描述。它是一個鐘形線(有時又叫高斯分佈),關於均值對稱,在兩邊向下無限延伸,理論上沒有邊界。正態分佈的99.73%的測度值位於 +3s 和
−3s 之間,這就是為什麼控制圖的邊界叫3σ 邊界的原因。
像摩托羅拉等公司的邊界是6σ 而不是3σ ,其好處如表20-3所示。邊界為6σ 時,每10億單位產品中只允許有2個錯誤。維持6σ 成本是非常昂貴的,除非成本可以分散於如10億單位的產品中。
圖20-3 正態(標準)分佈的屬性

續表
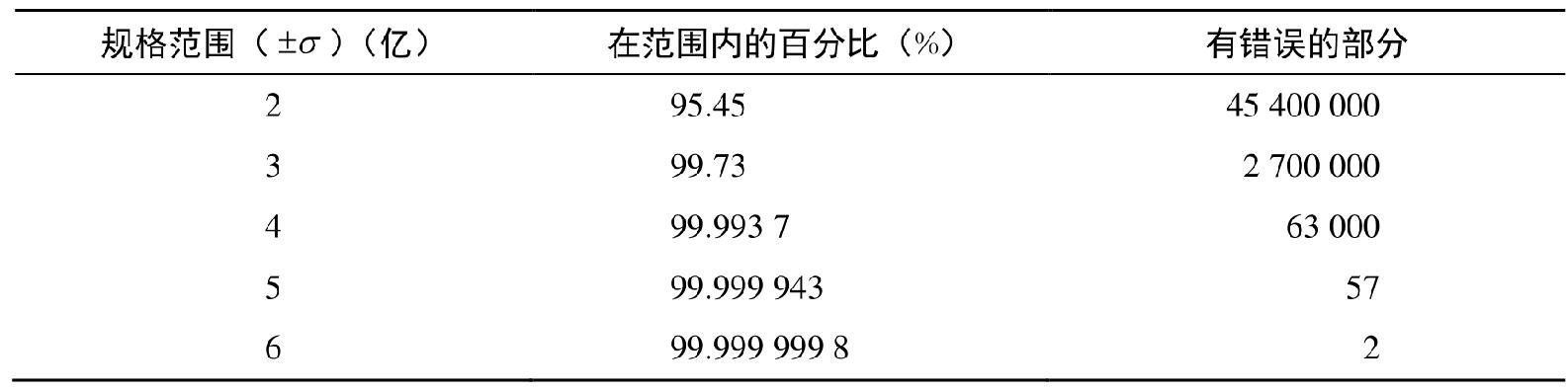
控制圖分析確定了內在過程變異和過程均值是否處於穩定水平,或者它們其中之一或兩者都處於統計之外(不穩定),或者是否應該採取適當的行動。用控制圖的另一個目的是區分過程內在和隨機變異及導致可指定原因的變異。隨機變異的來源一般作為共同原因。在過程沒有改變結構的時候,它們是不能隨意改變的。相反,特殊原因變異是在過程控制時對過程的糾正。
• 共同原因變異或變化。這種隨機變異出現在任何過程中,是過程內在的。只有當管
理者決定改變主要過程的時候,這種變異才可以被糾正。
• 特殊原因變異或變化。這種變異可以在局部或作業層得到控制。特殊原因在控制圖
中用一個點表示,它超出了控制限度範圍或者一致性趨近於控制限度。
2.控制圖的類型
PMBOK ® 指南,第6版
8.3.2 控制質量:工具與技術
正如數據有離散和連續兩種類型一樣,控制圖也有兩種類型:用於連續數據的變量圖和用於離散數據的屬性圖。每種類型的控制圖都可以用於具體類型的數據。表20-4總結了兩種類型的控制圖及其應用。
圖20-4 控制圖的類型和應用
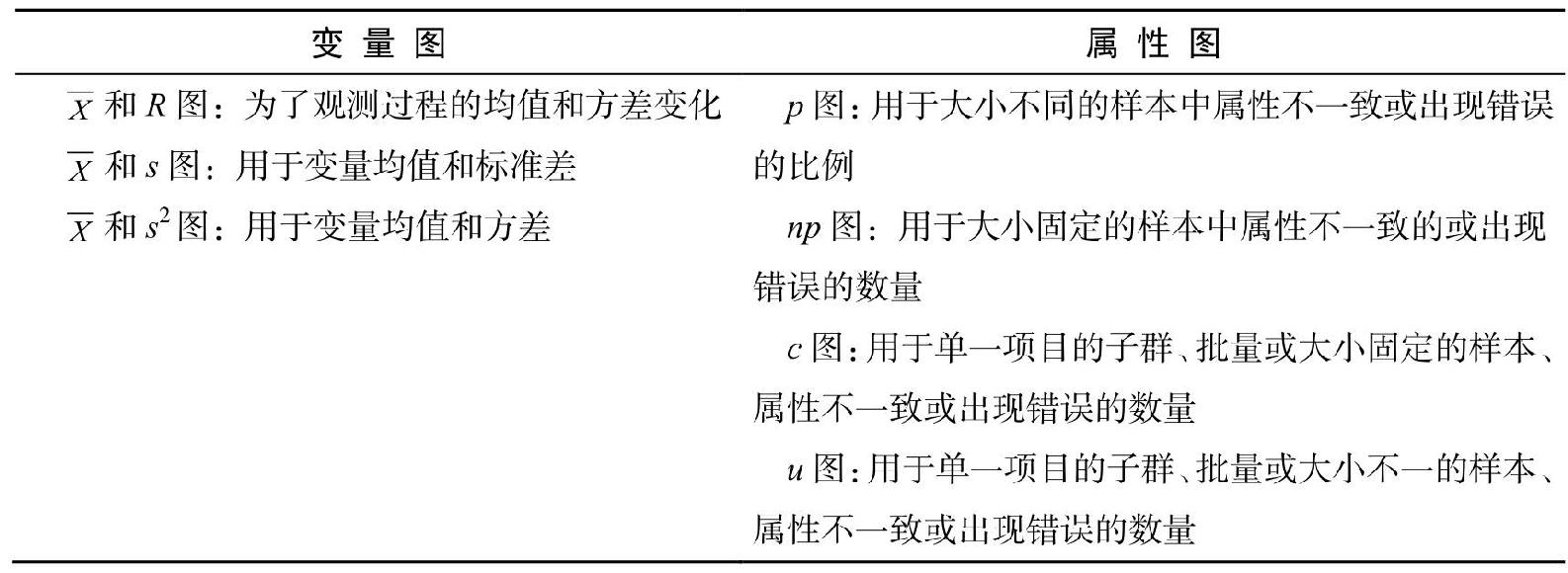
(1)變量圖。 變量控制圖是非常有力的工具。當過程的測度發生變化時,我們可以應用它。數據變量的例子有軸的直徑、電子輸出或支撐物的扭矩。
如表20-4所示, 和R 圖用於測度連續變量特徵的控制過程,如重量、長度、歐姆、時間、貨物容量。p 圖和np 圖用於測度和控制用樣本展示特徵的過程,當錯誤次數用比例表示的時候用p 圖,用數字表示的時候用np 圖。c 圖和u 圖用於測度單一項目的錯誤數量或比例,樣本大小或區域固定時用c 圖,樣本大小或區域不固定時用u 圖。
(2)屬性圖。 控制圖通常根據變量來考慮問題,但也有根據屬性考慮問題的。屬性變量有兩個值(一致/不一致,通過/未通過,做/不做,具備/缺少),但是它們也可以統計、記錄和分析。這樣的例子有具備所要求的標籤、具備所需要的支撐物、具備焊接熔滴或電路連續性。如果結果用簡單的是/否形式記錄的話,我們也可以將屬性圖用於可測度的特徵,如用測量/不測量測度軸直徑的一致性、用目測或儀器測量極限邊際的可接受性。
當屬性為檢測的基礎時,可以將控制圖用於作業。其方式在某種意義上同變量的使用方式相似,但有一定的區別。處理被拒絕樣品的比例時,控制圖的類型被稱為p 圖;處理被拒絕的數量時,被稱為 np 圖。如果產品有多個不一致性,並且所有這些不一致性都按照固定大小的子群來統計,控制圖則被稱為c 圖;如果每單位不一致性的數目是利益的數量,控制圖則為u 圖。
控制圖的(Shewhart技術)功用在於它確定下述問題的能力:變異原因是特殊原因(可以在過程層被影響的)還是共同原因(需要管理層面的變更)。控制圖的信息可以用於指導工程、技術、管理者以完成預防和糾正行動。
為了保持令人滿意的控制狀態,統計控制圖的應用目的在於研究正在進行的過程。相反,後期檢測的目的是找出錯誤。換句話說,控制圖致力於防止錯誤而不是檢測和拒絕錯誤。這看起來是合理的,在實踐中也得到了驗證,即經濟和效率是通過採取預防措施而不是通過檢測實現的。
3.控制圖解釋
PMBOK ® 指南,第6版
8.3.2 控制質量:工具與技術
控制圖的變化和形式的不同有許多種可能的解釋。如果解釋正確的話,控制圖能夠告訴我們的東西更多,而不只是簡單的過程是否可控。經驗和訓練可以使我們增加提取考慮過程行為的線索的技能,統計指南是非常寶貴的,但是對所研究的過程有更多的瞭解對提高研究水平也很關鍵。
控制圖可以告訴我們什麼時候會有麻煩,但它本身不會告訴我們哪裡會出問題,或者會發現什麼原因。實際上,在許多情況下,控制圖的最大優勢之一就是它能告訴我們什麼時候不需要人為干預。有時,操作工人持續地做出小的改動,而不是使變量穩定地處於自然範圍內,這會造成不必要的變異。